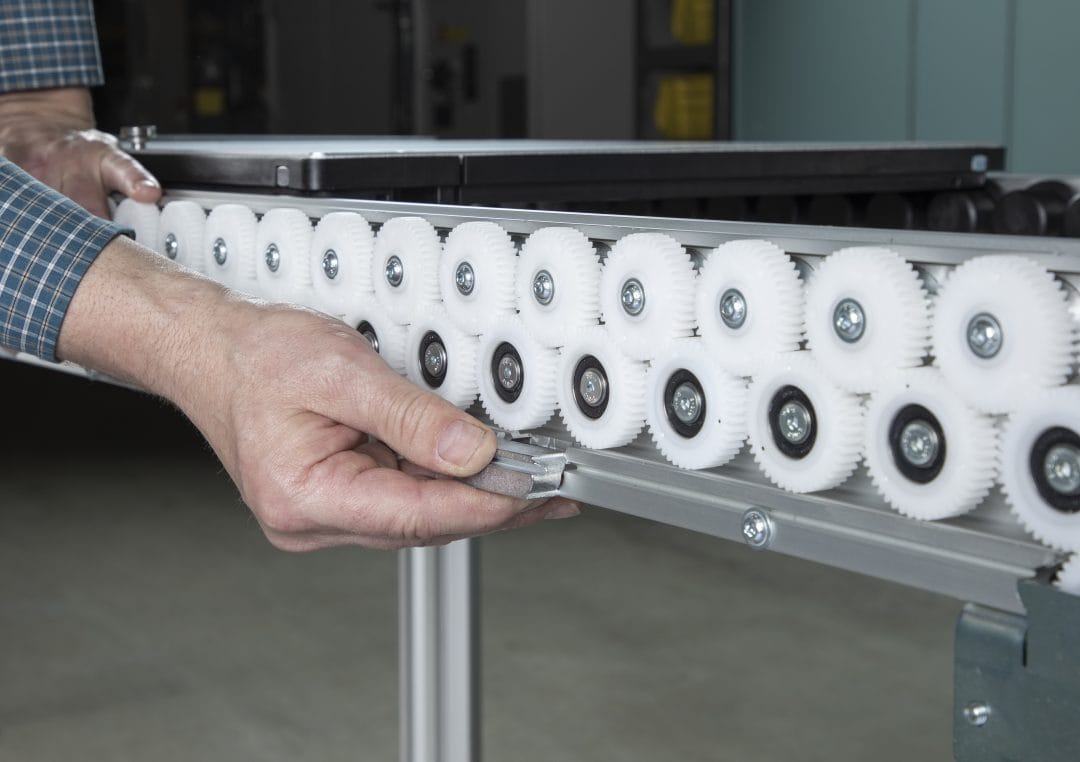
To keep up with continuously changing demand, manufacturers are facing the pressure to improve their process while still developing new products for consumers. This means that the machinery used in manufacturing must be able to adapt and change to meet new needs. That is where Dorner’s ERT conveyors come in.
Edge Roller Technology
Dorner’s ERT150 and ERT250 conveyors are innovative roller technology-driven conveyor systems for pallet and tray handling. The rollers are driven by an energy-efficient linear gearbox that provides added flexibility with motor positioning and zoning. ERT conveyors are easy to reconfigure in the field without the need for specialty tools or training. Here are a few ways these conveyors are designed to be adaptable to our customers’ needs.
Gearmotors & Gears
A major benefit of ERT conveyors is their reconfigurability. The ERT’s patent-pending gearbox allows for zone and slip-roller operation and is easily reconfigurable in the field. Simply removing a lower gear creates independent zones. As zones are created or adjusted, the drive shaft can be moved to different zones as needed for the application.
Gearmotors can also be easily moved along the ERT conveyor. The conveyor side rail is designed with machined openings, with removable plugs, at regular increments. If you need to move the gearmotor location to add a module, for example, you can do this at your facility without cutting or modifying the side rail. The motor on an ERT250 be relocated every 250 mm, and every 128 mm for the ERT150.
Reconfiguring zones and the motor position may be necessary if the application for the conveyor changes, if new modules are being added to the system, or if there are any other changes to the production process.
Drive Shaft Position
An additional option for reconfiguring the system lies within the drive shaft location. Rollers are situated evenly on each side rail, and the drive shaft can be moved to any set of rollers on the conveyor. In order to move, both sides of the drive shaft connect across the conveyor, typically between rollers. With this layout on the ERT150 and ERT250, there is approximately 4 mm and 10 mm of clearance below the pallet respectively.
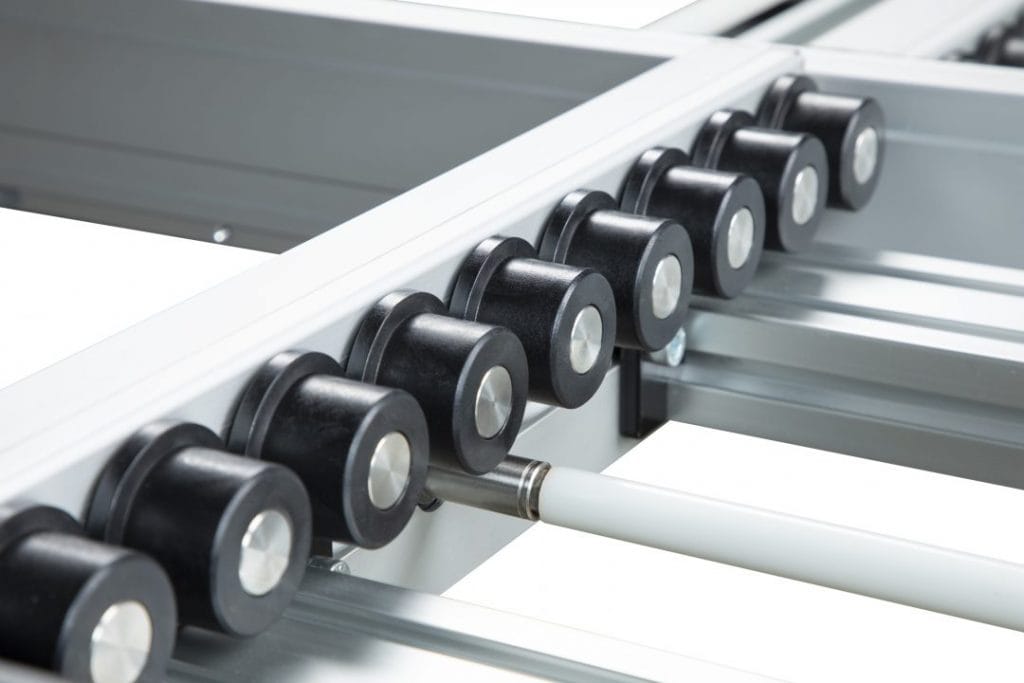
Optional lower drive shaft location shown here.
If the product simply sits on top of the pallet this level of clearance is acceptable. However, for applications where the product may need to drop below the pallet and additional clearance is needed, the drive shaft can be moved to the lower section, below the roller line. By moving the drive shaft to the fame below the roller, the clearance below the pallet is now increased up to 45 mm.
The main difference in mounting the driveshaft to the rollers versus the frame is that it can be moved to any of the rollers to aid in creating different zones in the field, whereas the drive shaft can only be mounted to one place on the frame. This is because the slot for the drive shaft is custom machined into the frame.
If an application calls for complete clearance, there is the option to remove the drive shaft completely and instead add a second gearmotor. Each side rail and motor would run independently, but one of the benefits of the ERT’s controller is that it can drive two gearmotors simultaneously. In an application with two motors on each side rail, the two motors will be electronically synced to maintain accuracy during pallet transfer.
Increase Adaptability with Dorner’s ERT Conveyors
As our team continues to develop new conveyance technology, conveyor systems are becoming more flexible and customizable to fit the needs of a wide range of applications. Most importantly, with an ERT conveyor, the system is easily reconfigurable in the field to adapt to help our customers continue to grow and evolve.
Learn more about Dorner’s ERT Conveyors.