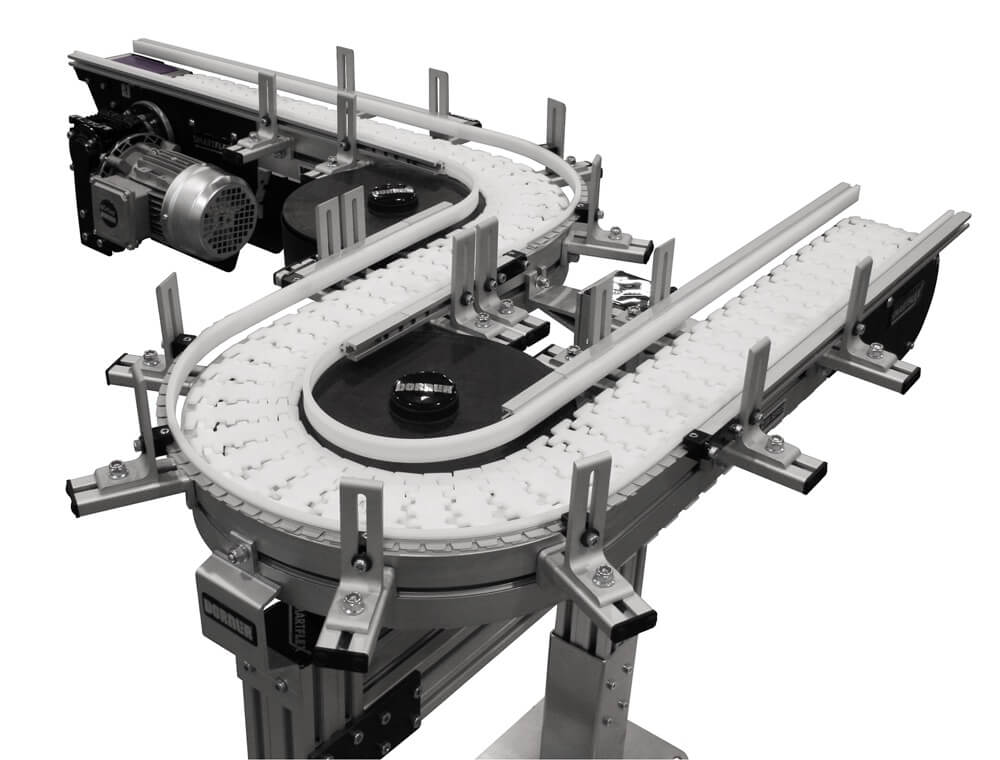
Cutting Downtime and Increasing Throughput for Over 50 Years
Dorner is a global manufacturer of industrial conveyor systems, offering a wide range of automated conveyor solutions to help companies optimize material handling and industrial automation processes.
With decades of experience as a low-profile conveyor manufacturer, serving industries from automotive to food and beverage, our reliable, durable conveyor platforms handle everything from heavy-duty loads to delicate products. Our custom-engineered conveyor solutions ensure each system meets your specific application requirements—enhancing efficiency, safety, and throughput across the board.