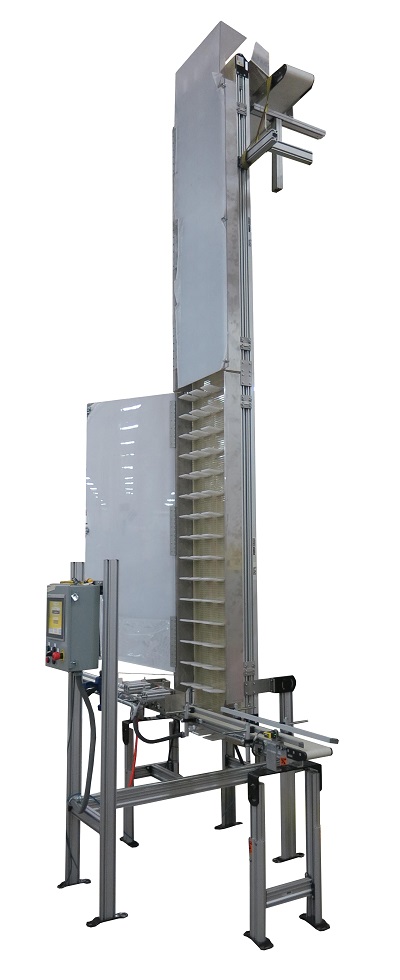
Manufacturing lines aren’t always on a single level. For this paper company, the product accumulator was 20 feet above the paper cutter on the ground level. To transport the paper rolls between machines, Dorner created an elevator to move the product vertically.
The rolls of paper travel from the paper cutter down a belted 2200 Series conveyor equipped with photo-eyes, a retractable end stop and a pusher. The paper rolls first pass by a photo-eye which measure the length of the roll. If the roll is the incorrect length, the retractable end stop will retract and the roll will continue to the end of the conveyor and be discharged onto a table.
If the roll is the correct length, the end stop will extend and position the roll in front of the vertical conveyor. Once the photo-eye detects the roll, a pusher will move the roll onto the vertical conveyor.
The vertical conveyor is a custom engineered 3200 Series Precision Move using two 12” wide belts with custom cleats. The cleats are angled backwards to allow for the paper roll to be held in place while being conveyed upwards.
One the roll has moved onto the vertical conveyor, the 3200 Series will index one cleat pocket, making room for the next roll to load. Once the rolls reach the top of the conveyor, they will discharge one at a time onto a series of 3200 Series belted conveyors.
The rolls then travel down the three 3200 Series belted conveyors until they hit an end stop on the final conveyor. Once three rolls have loaded onto the final conveyor, a pusher will move the rolls into the accumulator.