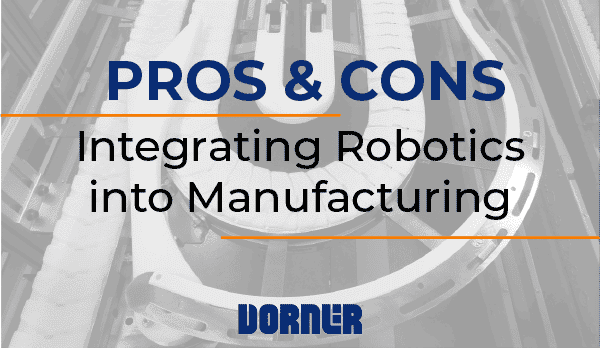
As technology continues to progress towards new innovations in automation, it is no surprise that the robotics industry is booming. This is especially true for industrial robotics designed for the manufacturing industry, which is already surpassing the automotive industry as the largest user of industrial robots. Where tasks are repetitive or dangerous for human operators, robots are an ideal option.
There are a wide variety of applications for robot and automated integration, from food packaging and medical device production to consumer goods assembly and metal fabrication. However, as with any new technology, it’s important for businesses to evaluate their unique applications and the pros and cons of integrating robotics into that process.
Pro: Improved Productivity & Efficiency
A study conducted by Vanson Borne reports that 23% of unplanned downtime in the manufacturing industry comes down to human error. There are many factors that contribute to this staggering number, particularly the wide breadth of machinery operators need to be properly trained in. The programmability of industrial robotics means they can be installed to perform a huge range of tasks and can start on day one after installation, where an operator would need time to train.
An automated production system with conveyors and robots can also move faster and with more consistency than human operators. They can typically run nonstop, as well, drastically improving production and throughput. Combined with the fact that automated systems can operate with a high degree of accuracy, they have been shown to improve efficiency and reduce waste in both materials and time.
Pro: Improved Quality
Accuracy and repeatability are integral to quality, and industrial robots are designed to deliver both. With the high degree of accuracy that robots deliver in assembly and manufacturing, there are fewer mistakes and fewer wasted products.
Additionally, in sanitary and cleanroom environments, the use of specialized robotics and automation reduces or completely eliminates human operators’ interaction with product, which in turn significantly reduces the risk of contamination.
Programmable precision conveyors allow for complete control of product as it is moving between and through other machinery and robotics stations. With a high rate of accuracy and repeatability, a complete automated system of conveyors and robotics helps to improve quality and increase the throughput of the production line.
Pro: Easily Integrate with Conveyors
When you have precision conveyor systems from Dorner, it is easy to integrate robotics into your manufacturing process. 2200 Series conveyors are a certified UR+ Solution and are proven to simplify the robotics integration process.
Integration is made even easier when conveyors and robots are run on the same controller or programmed together. This ensures that the product is in the proper position at the exact right time to interface with the robot.
Pro: Increased Flexibility
Current consumer demands require businesses to be flexible in the product they produce and in turn how they produce it. Between design changes, changes in materials, and new product development, manufacturing lines can be in constant flux which requires frequent re-training of staff.
Automated systems that are controlled by software can be easily reprogramed or have their current procedure adjusted to meet the new product requirements. Many new systems are even capable of storing multiple production programs for quick changeover between product types.
Pro: Increased ROI
While there can be a high initial cost to implementing and integrating robots and automated conveyance systems, the increased productivity and efficiency help increase revenue and overall return on investment. With increased speeds, improved quality, and a reduction in downtime, automated manufacturing with conveyors and robotics can drastically improve production and overall revenue for a business.
Automating the repetitive processes of production also frees up staff for more challenging or engaging tasks that require creativity and problem-solving. Not only can this reduce labor costs, but it also allows staff to use their time improving products and processes, and growing the business as a whole.
Con: High initial investment
The obvious downside to implementing robotics and automation in manufacturing is the high initial investment. Robotics are highly customizable, but that means that the price tag attached to building and programming a system can be more than a company is comfortable investing for one portion of their production line.
Con: Expertise can be scarce
Related to the high initial investment, expertise in robotics manufacturing and maintenance can be scarce. While the industry is quickly growing, it is still a niche area, and the knowledge to create or adjust programming can be hard to find outside of the OEM of the robotic system.
The lack of expertise also means that staff will need to be trained by the OEM on proper maintenance or operation of the robotic system. This may add additional time and cost to the initial implementation of the system as well.
Con: Technology Limitations
Finally, there are still some limitations to existing robotics technology when it comes to manufacturing processes. As of today, robots are ideal for repetitive tasks, but some production processes require a higher level of complexity than robots can accomplish.
Dorner is Here to Help!
Considering implementing robotics and automation processes into your manufacturing line? Dorner’s precision conveyors are designed to easily integrate with both human and robot interfaces and are programable for easy automation. Our team of application engineers can walk you through the available options and will ensure your new automation conveyor system meets the needs of your application. Contact our team to get started!