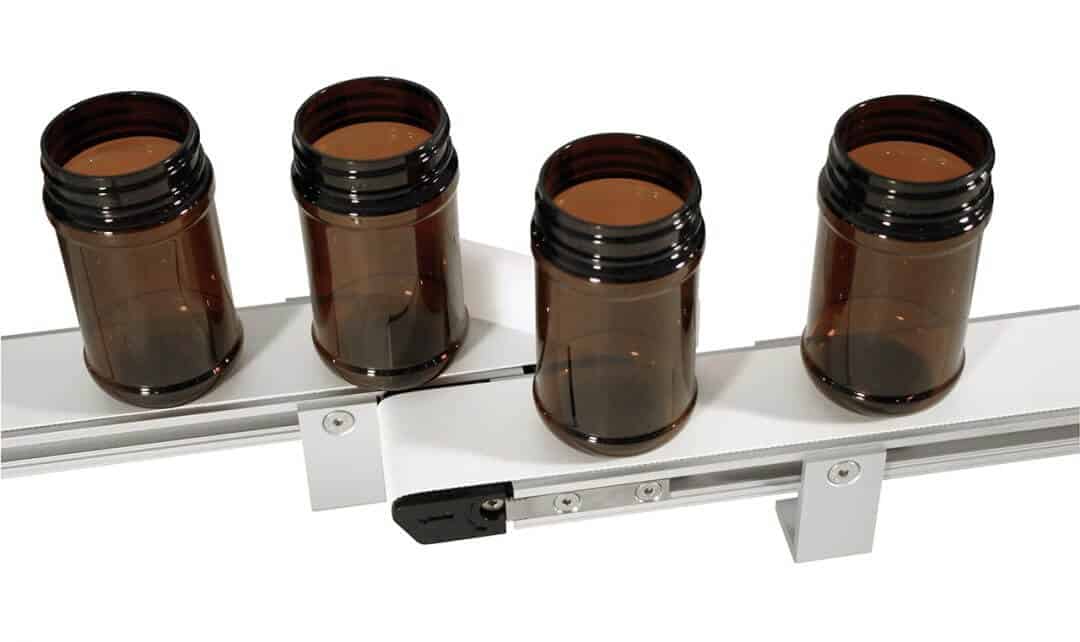
Small conveyor belts are revolutionizing the way companies handle product movement in industrial automation, medical device manufacturing, e-commerce, and more. As products become more compact—and as manufacturing spaces shrink—miniature conveyors and low-profile conveyors offer a perfect balance of precision, space efficiency, and integration flexibility. In this article, we’ll explore five key applications where small conveyor belts truly shine, discuss why they’re essential, and reveal how Dorner—with products like the 1100 Series—can help optimize your production line.
The Importance of Small Conveyor Belts
In modern manufacturing, efficiency and precision are top priorities. Whether you’re assembling circuit boards, packaging delicate medical devices, or inspecting lightweight products, having a compact conveyor system can significantly streamline workflow. By occupying minimal floor space while delivering accurate product positioning, small conveyor belts solve real-world automation challenges. Let’s look at five specific areas where they make a big impact.
Miniature and low-profile conveyors stand out because they:
- Conserve Space: Ideal for tight production floors and cleanroom environments.
- Deliver Precision: Provide accurate tracking and positioning for delicate or small parts.
- Support Specialized Belting: From FDA-approved options for pharmaceuticals to ESD-safe materials for electronics, you can customize the belt surface to your product.
- Integrate Seamlessly: Pair easily with robots, sensors, and overhead machinery, maintaining consistent throughput and quality.
- Offer Broad Industry Applications: Perfect for industries like medical, electronics, pharmaceutical, food handling, and more.
Dorner’s 1100 Series, for example, is one of the world’s most compact conveyors—featuring a ¾-inch frame height. Its tight-transfer nose bar option makes it ideal for handling small or fragile products, with a minimal footprint to transport product through machinery.
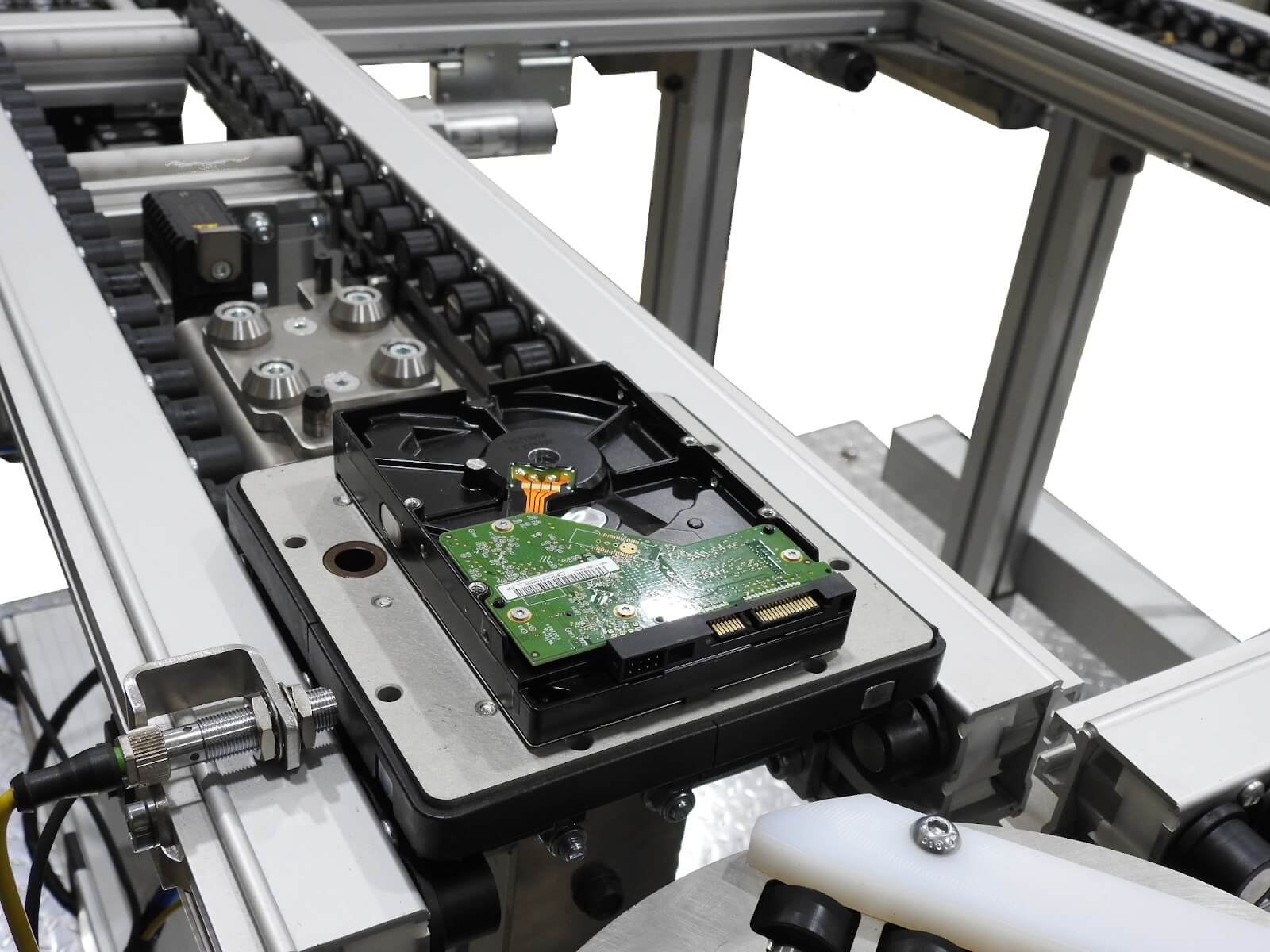
Application #1: Electronics Assembly & Testing
Why It Matters
Electronics manufacturing involves assembling tiny circuit boards, microchips, and sensor components—all requiring precise indexing for processes like robotic pick-and-place, soldering, or automated inspection. Errors during transport can lead to damaged boards or misaligned parts.
How Small Conveyors Help
- Gentle Handling: Lightweight belting and low-profile frames reduce vibration that could damage sensitive electronics.
- Compact Footprint: Fits under overhead equipment or inside test stations without impeding operator access.
- Accurate Indexing: Servo-driven conveyors or Dorner’s Precision Move technology support high-resolution part placement.
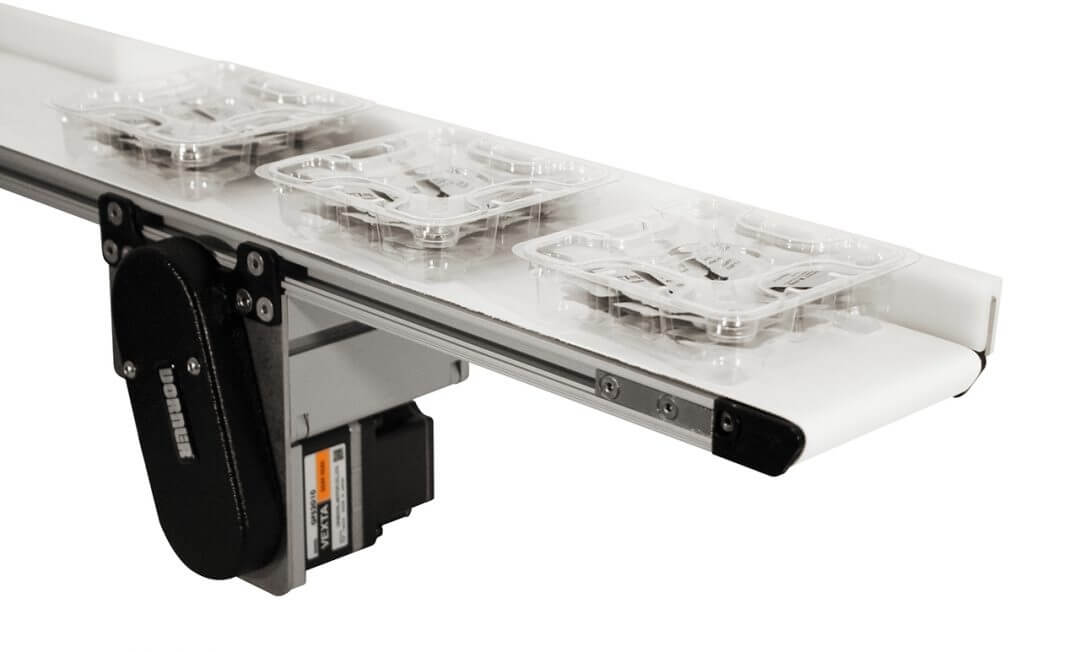
Application #2: Medical Device & Pharmaceutical Handling
Why It Matters
In medical device manufacturing—particularly for implantables, diagnostic equipment, or pharmaceutical packaging—stringent FDA and cleanroom standards must be met. Conveyors need easy cleaning features, static protection, and gentle transport to avoid contamination or damage.
How Small Conveyors Help
- Space-Efficient Designs: Low-profile frames save room in labs or cleanrooms, where every inch matters.
- High Precision: Delicate devices like syringes, vials, or micro-sensors are consistently positioned for assembly or inspection.
Dorner Tip: Models like the 1100 Series are Cleanroom Class 100 rated (in unloaded tests) and can incorporate ESD-safe materials, making them ideal for medical device or pharma production lines.
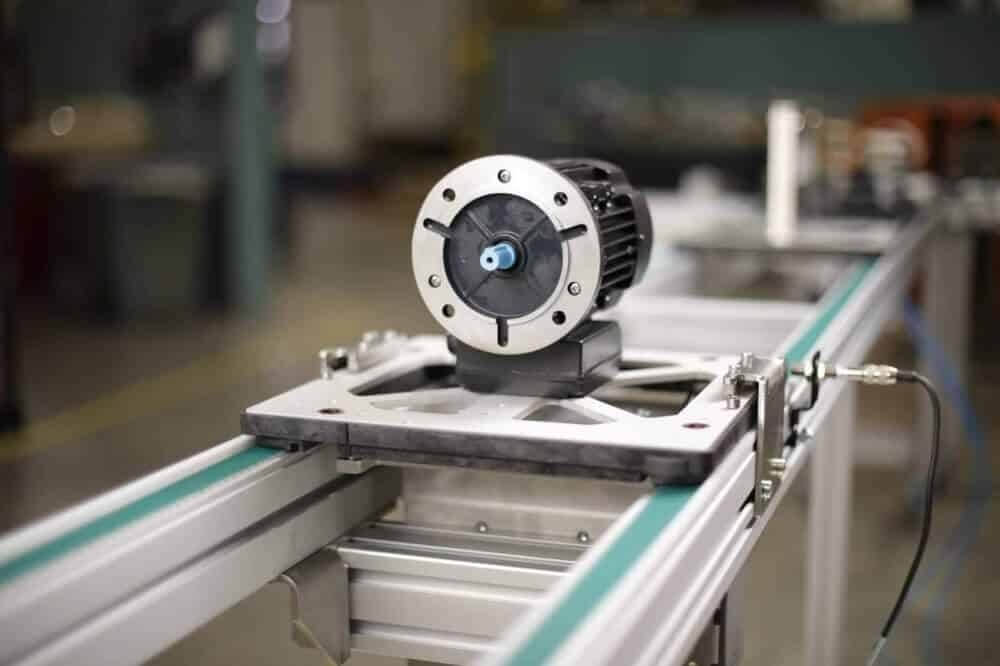
Application #3: Robotics & Pick-and-Place Integration
Why It Matters
Robotic arms (like automation integrators) thrive on consistency and precise part alignment. For small or lightweight items, even the slightest jostle can cause pick errors. Proper feeding and alignment are crucial for maximum efficiency.
How Small Conveyors Help
- Consistent Part Spacing: Servo-driven or timing belt-driven conveyors can maintain precise product gaps for quick robot pickups.
- Integration Flexibility: Low-profile platforms fit under robotic arms without restricting movement.
- Programmable Speeds: Synchronize conveyor speed with robot cycle times to minimize idle or wait times.
Dorner Tip: Many Dorner conveyors use a universal T-slot for easy mounting of sensors, guide rails, or robotic end-effectors—further enhancing automation versatility.
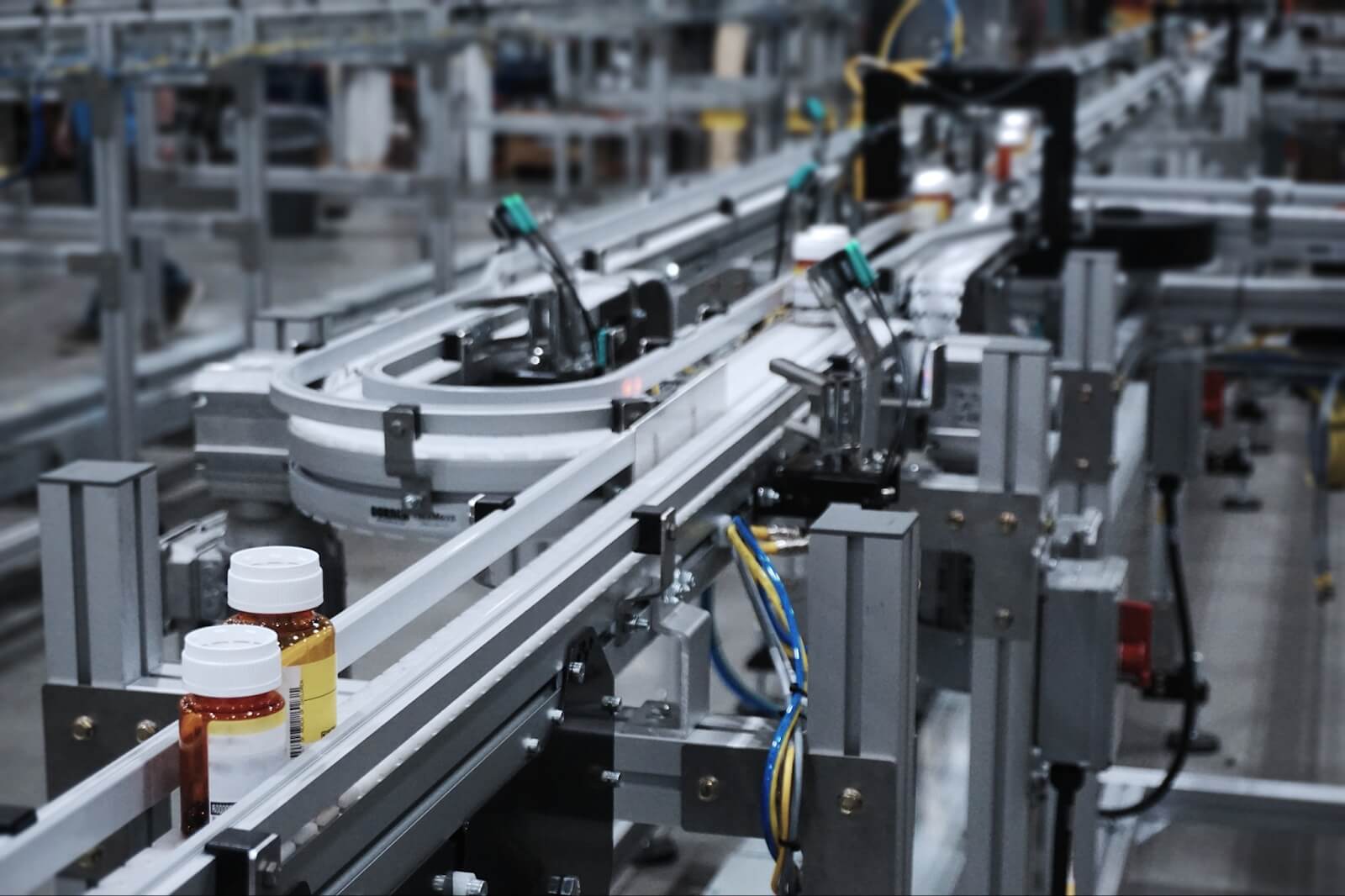
Application #4: Packaging & Labeling for Small or Lightweight Products
Why It Matters
From cosmetics to medical testing kits, packaging lines often deal with tiny or flexible pouches, blister packs, or bottles. Misalignment leads to misapplied labels, scanning errors, or even product jams.
How Small Conveyors Help
- Smooth Transfer: Nose bar designs transfer small pouches or blister packs without toppling or dropping valuable product through gaps in equipment.
- High-Speed Precision: Supports fast labeling, sealing, or scanning with consistent product orientation.
- Modular Layouts: Flexible chain conveyors or tight-radius belt conveyors can navigate facility constraints and connect multiple packaging stations.
Dorner Tip: For pharmaceutical or nutraceutical packaging, Dorner’s 2200 Series or FlexMove can provide both speed and gentle handling, often paired with integrated vision systems for quality checks.
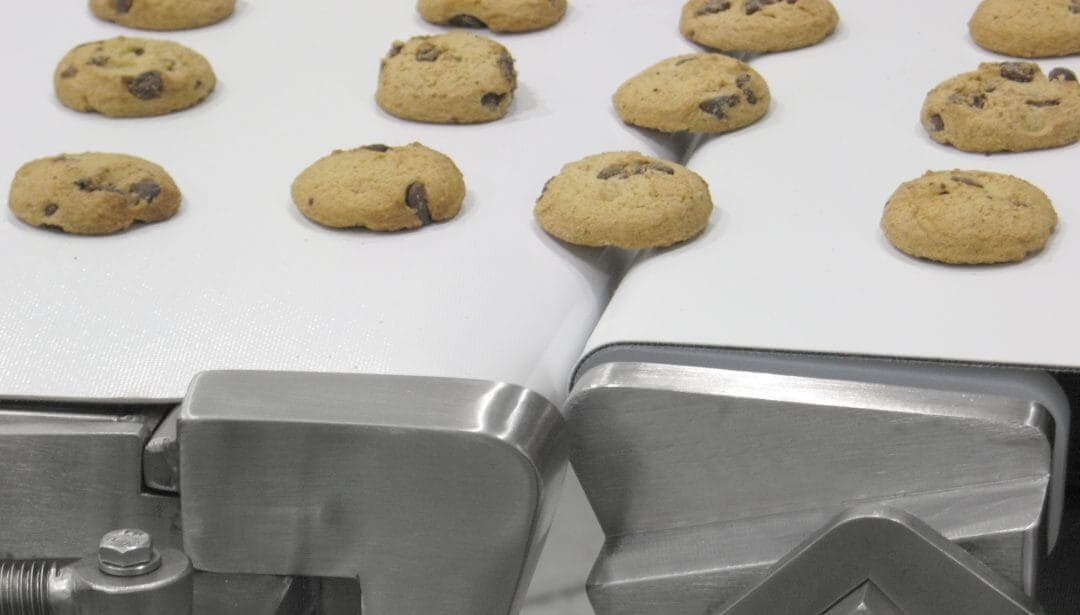
Application #5: Food & Beverage Sampling Stations
Why It Matters
Food and beverage companies often set up small-scale lines for new product sampling or test runs—especially in pilot plants or R&D labs. Compact conveyors help maintain hygiene while managing various test batches.
How Small Conveyors Help
- Washdown-Ready Designs: Stainless steel frames and FDA-approved belts can handle washdowns for sanitary compliance.
- Easy Belt Changes: Quick-release mechanisms let you swap out belts for different sample runs.
- Minimal Footprint: Freed-up floor space for additional equipment or quality-control stations.
Dorner Tip: Consider the AquaGard LP conveyor for lightweight packaged foods or confectionery items. Its low-profile design and fast belt change features make it ideal for test lines and small-batch runs.
Key Factors to Consider When Choosing a Small Conveyor Belt
- Belt Material & Surface Texture
- FDA-approved for food & pharma, ESD-safe for electronics.
- Smooth or cleated surfaces, depending on incline or product type.
- Frame Construction & Profile Height
- Aluminum or stainless steel frames.
- Low-profile designs (like the 1100 Series’ ¾-inch frame height) for table-top or inter-machine processes.
- Cleanliness & Compliance
- Cleanroom-rated or washdown-ready designs.
- Ability to handle regular sanitization without degrading the conveyor or belt.
- Precision & Speed Requirements
- Servo controls for indexing.
- Timing belt or direct drive for high-speed and accurate part positioning.
- Modularity & Future Upgrades
- Reconfigurable layouts with FlexMove or Dorner pallet systems.
- Universal T-slots for easy addition of sensors, rails, or diverters.
Next Steps With Dorner
Small conveyor belts bring big benefits to automation, precision, and throughput—especially for industries handling miniature parts, delicate items, or cleanroom products. From electronics assembly to food sampling, medical devices to robotic automation, these low-profile systems easily integrate into your workflow, saving space and ensuring high-quality product movement.
Ready to explore Dorner’s solutions for miniature conveyors, flexible chain systems, or cleanroom-rated models? Our experts can guide you to the best small conveyor belt setup for your exact application—whether you need a customizable belt surface, servo-driven precision, or a washdown-capable conveyor for sanitary compliance.
Contact Dorner today or start designing your own custom conveyor with DTools, our intuitive online CAD/Configurator platform. Let’s see how small conveyor belts can transform your automation processes!