Engineered Solutions
Bottomless Conveyors
-
-
Flexible Packaging - Pinch Transfer
-
-
Bottomless conveyors provide a simple solution for accessing the underside of a product for a range of applications. These applications include inspection, printing, labeling and edge sealing.
Sometimes referred to as side gripping conveyors, bottomless conveyors are compatible with boxes and flexible pouches or packages. These conveyors are also called horizontal conveyors, or horizontal mounted conveyors, as they are mounted horizontally.
With bottomless conveyors, two conveyors—either sold with an adjustable option for a variety of product sizes or preset—are mounted on the edge. If using a conveyor with an adjustable option, once the conveyors are adjusted to the proper width, products are “locked” in place and can transfer to the next phase of your production line.
Bottomless conveyors can also be used in line over another conveyor to pace product.
How Do Bottomless Conveyors Work?
- Bottles
- Boxes for adding labels or inspection
- Product inspection
- Product pacing
- Box sealing
- Inkjet coding for printers
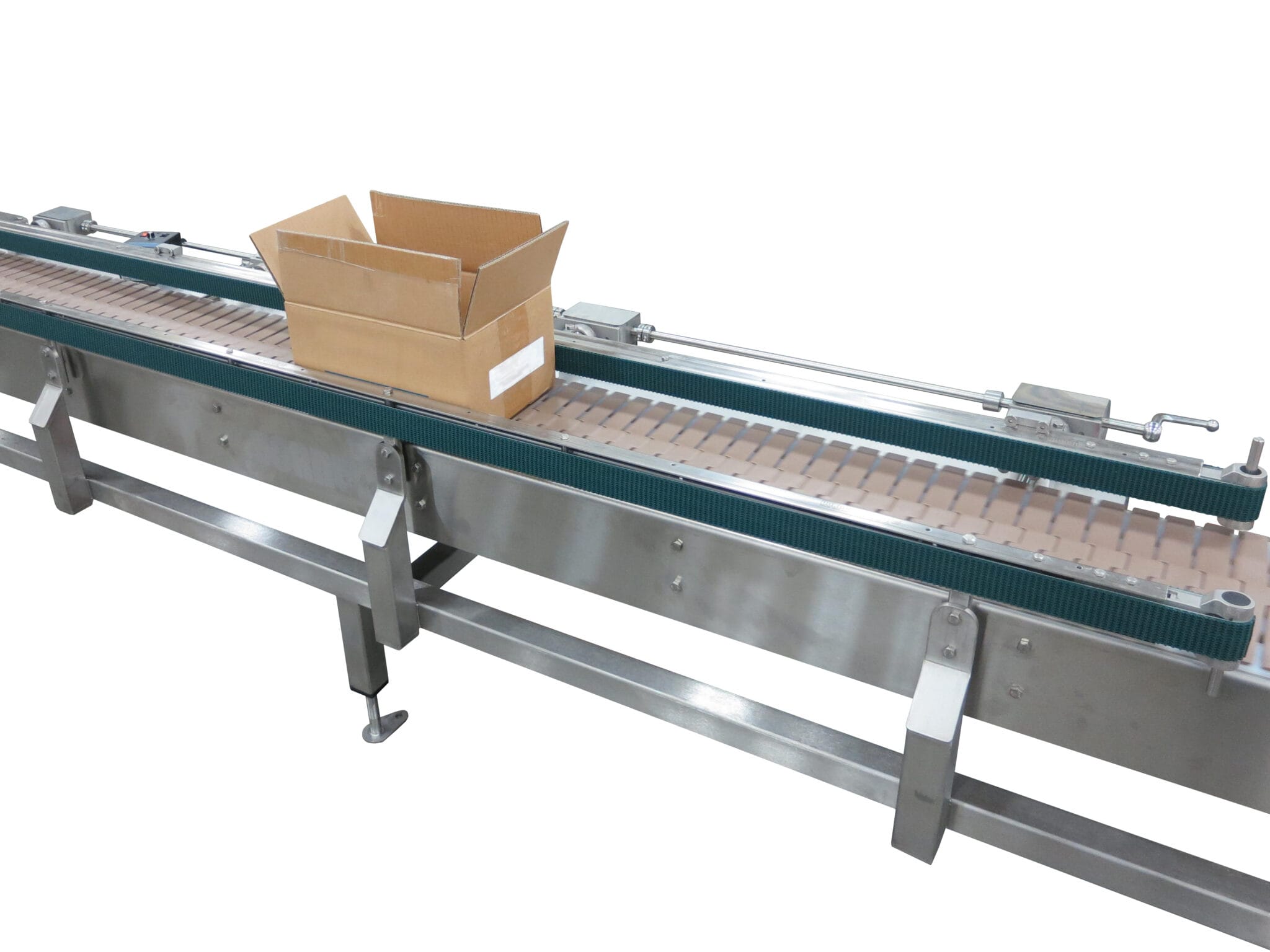
Let’s explore these applications and how bottomless conveyors play a role in them.
Bottling Operations
One Dorner customer faced challenges in consistently sealing wine bottles its facility produced. This customer needed to evenly apply heat completely around the seal at the top of the bottle.
The Dorner team made use of a 2200 Series conveyor along with a mainline chain conveyor, with the 2200 Series conveyor mounted on its side and running parallel with the main line conveyor.
A high-friction Dorner Type 64 belt enabled the conveyor to spin the bottle a complete revolution as it moves through a heat tunnel. This full spin enables heat to be evenly applied around the whole seal.
Boxes for Adding Labels
Product Inspection
Box Sealing
Inkjet and Laser Printer Coding for Printers
Product Pacing
Dorner’s bottomless conveyors may be used with a Clamping Module on our FlexMove® conveyor systems to pace product as part of accumulating applications. The Clamping Module works well with totes, boxes, bottles and containers that are round, square or rectangular in shape.
As products pass through the Clamping Module, pre-programmed photo sensors trigger a pneumatic-clamping actuator mounted on each of the conveyor’s sides. The Clamping Module produces a gap of about a single product length. With this kind of setup, product must be able to withstand minimal back pressure and squeezing force.
Dorner’s 2200 Belted Conveyors are also used to pace product.
Additionally, our AquaGard 7200 Conveyors are used as part of a similar application: product stablization. When packaging product into boxes, it’s often critical to ensure the box is in the needed position, especially when a robot is taking care of packing. Our AquaGard 7100 Series sanitary conveyors are built with two conveyors on top that act as “squeezers” for various box sizes, helping ensure boxes are properly positioned before being filled.
The 7100 Series conveyors run alongside another conveyor that moves product, and a picking robot places product into the box as it travels down the line. This squeezing effect keeps the box in place as it travels along, and the robot can be certain of the box’s precise location.
The two “squeezing” conveyors are part of Dorner’s AquaGard 7200 Conveyor Series, comprising our low-profile sanitary conveyors.
Bottomless Conveyors Features and Benefits
- Holds product firmly, without damaging it, for inspection, printing or labeling.
- Provides easy inspection access to the bottom and top of the product.
- Manual and motorized adjustment options are available for flexibility in production.
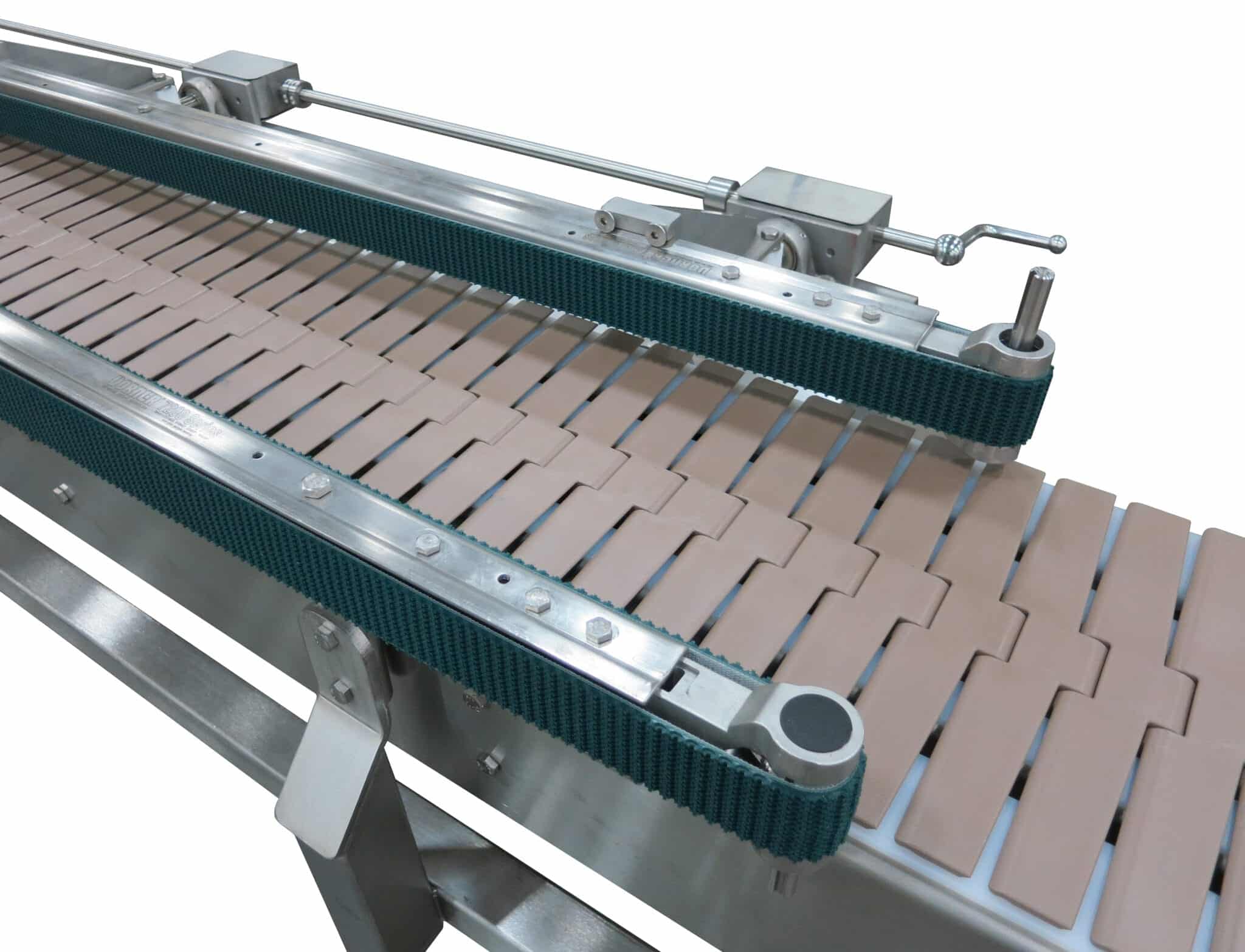