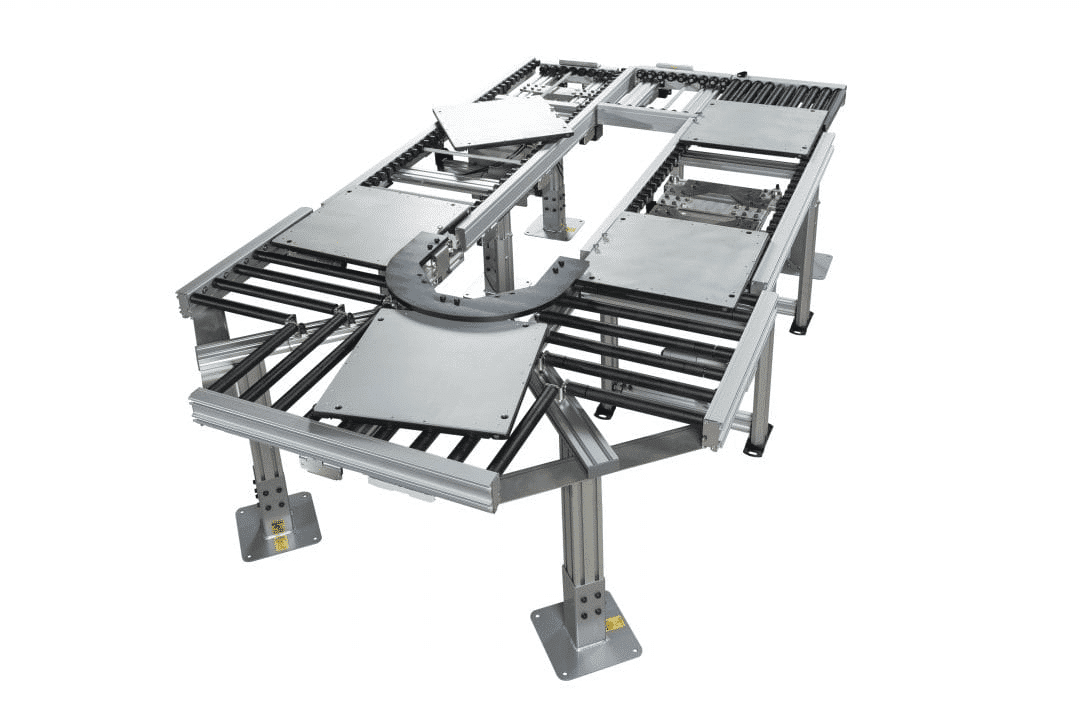
The medical device manufacturing industry faces a unique set of challenges. Precision, cleanliness, and efficiency are not just goals — they’re necessities. And as devices become increasingly complex and miniaturized, some traditional manufacturing processes may struggle to keep pace with the demanding requirements of the medical device sector.
Enter Edge Roller Technology (ERT) conveyors — a game-changing solution that has helped to reshape the landscape of medical device production. These innovative systems are specifically designed to address the needs of the industry, offering a level of control, cleanliness, and adaptability that was previously difficult to achieve.
ERT conveyors (like Dorner’s ERT150 & ERT250) offer unique benefits that directly address key challenges in medical device manufacturing. From enhancing precision and maintaining cleanliness to improving efficiency and supporting regulatory compliance, ERT systems continue to improve the way we produce the life-saving devices of today and tomorrow.
Understanding Edge Roller Technology (ERT)
As a medical device manufacturer, you’re constantly battling the limitations of traditional conveyor systems. You’ve faced the frustration of contamination issues, the headache of inflexible production lines, and the constant pressure to increase precision while reducing costs. To stay competitive and ensure patient safety, you need a conveyor solution that doesn’t just move products — it elevates your entire manufacturing process. Here’s how it works:
- Open-frame design. The edge rollers and beltless design allows any potential particles or dropped parts will fall through to the floor, eliminating the risk of jamming the conveyor or contaminating products.
- Edge-driven movement. Pallets or products are moved by contact with these rollers along their edges, minimizing surface contact and potential contamination.
- Modular design. ERT conveyors are built with a modular approach, allowing for easy customization and reconfiguration.
Key features of ERT conveyors include:
- Precision control. Individual motorized rollers allow for precise start/stop control and positioning.
- Low particle generation. The belt-free design significantly reduces debris production caused by friction.
- Flexibility. Modular construction enables easy system reconfiguration and expansion.
- Energy efficiency. 24V DC motors on all drives and modules, when coupled with frictionless technology, result in energy consumption less than half of most other conveyor systems.
Compared to other conveyor systems, ERT conveyors offers several advantages for medical device manufacturing:
- Improved cleanliness. Without a continuous belt, there’s less opportunity for particle generation and contamination.
- Enhanced control. The ability to create discrete zones of movement allows for more precise product handling.
- Reduced maintenance. Despite having more moving parts, the system’s design allows for quick individual roller replacements and eliminates belt-related maintenance, significantly reducing overall downtime and long-term costs.
Precision and Control in Medical Device Manufacturing
Every electronic medical device produced has the potential to significantly impact a patient’s life, making accuracy a critical factor at every stage of production. The challenge lies in consistently achieving and maintaining a level of precision that ensures the safety and efficacy of each device.
Consider the following examples:
- Implantable Insulin Pumps: These devices must deliver precise amounts of insulin at exact intervals. A deviation of even a fraction of a milliliter could lead to severe hypoglycemia or hyperglycemia in diabetic patients.
- Neurostimulators: These devices deliver electrical impulses to specific areas of the brain or nervous system to treat conditions like Parkinson’s disease or chronic pain. Precision in their manufacture ensures that stimulation is delivered to the exact intended location, avoiding potential side effects or reduced efficacy.
- Robotic Surgical Systems: The components in these systems must work in perfect harmony to translate a surgeon’s hand movements into precise actions inside a patient’s body. Any inaccuracy could lead to surgical complications.
- Delicate Electronics: Many medical devices contain sensitive electronic components that require protection during manufacturing. The ERT’s shock-free and static-dissipative qualities provide an ideal assembly platform, safeguarding these critical elements from damage that could affect device performance.
Moreover, the regulatory landscape in medical device manufacturing is ever-evolving and increasingly stringent. Bodies like the FDA in the United States and the EMA in Europe require manufacturers to demonstrate consistent precision and reliability in their products.
For instance, the FDA’s Quality System Regulation (21 CFR Part 820) mandates that manufacturers establish and maintain procedures for monitoring and control of process parameters for validated processes to ensure that the specified requirements continue to be met.
The stakes are high: a recall due to manufacturing inconsistencies can cost a company millions of dollars, damage its reputation, and most importantly, put patients at risk. In 2021 alone, the FDA reported over 3,000 medical device recalls, many of which were related to manufacturing issues.
The Precision Challenge in Medical Device Manufacturing
Electronic medical devices require extraordinarily tight tolerances. Even tiny inaccuracies can have serious consequences. For instance, a misalignment of just a fraction of a millimeter in a pacemaker’s components could affect its functionality and reliability. Manufacturers face several key challenges in maintaining precision:
- Miniaturization: As devices become smaller, the margin for error decreases.
- Complexity: Modern medical devices often involve intricate assemblies of numerous components.
- Scale: High-volume production makes maintaining consistent precision more challenging.
- Regulatory compliance: Strict industry standards require documented precision in manufacturing processes.
Edge Roller Technology (ERT) Conveyors: A Precision Solution
Thankfully, Edge Roller Technology (ERT) conveyors have emerged as a solution to address these precision challenges. Here’s how ERT conveyors contribute to precision in medical device manufacturing:
1. Accurate Positioning
ERT conveyors use individually motorized rollers that allow for precise start/stop control. This feature enables:
- Exact positioning of components or devices
- Repeatable accuracy across production runs
- Fine-tuned control over product movement
2. Zoning Capabilities
ERT systems can be divided into multiple, independently controlled zones. This design allows for:
- Precise movement and positioning throughout the production process
- Separation of different manufacturing stages on a single conveyor
- Customized and reconfigurable handling for different components or processes
3. Smooth Transitions
The roller-based system of ERT conveyors provides smooth acceleration and deceleration. Benefits include:
- Reduced risk of component displacement during transport
- Minimized vibration, crucial for delicate components
- Consistent handling throughout the conveyor system
Impact on Medical Device Manufacturing
The implementation of ERT conveyors in medical device manufacturing has several notable effects:
- Increased accuracy: The precise control offered by ERT systems helps maintain consistent quality across production runs.
- Reduced errors: Smooth handling and accurate positioning minimize the risk of component damage or misalignment.
- Improved efficiency: Zoning capabilities allow for optimized production flow and reduced downtime.
- Enhanced traceability: The ability to control and monitor each stage of conveyor transport supports better quality assurance and regulatory compliance.
“In medical device manufacturing, precision isn’t just about quality—it’s about patient safety. ERT conveyors represent a significant leap forward in our ability to maintain accuracy throughout the production process. This technology is changing the game for complex devices like implantable sensors and robotic surgical tools.” – Dorner expert
Maintaining Cleanliness In Controlled Environments
Cleanliness is paramount in medical device manufacturing. The production of these sensitive devices requires controlled environments to prevent contamination that could compromise product integrity or patient safety.
ERT conveyors excel in maintaining the cleanliness standards required for medical device production:
- Minimal contact points. The edge-driven design means less surface contact with the product, reducing the risk of contamination.
- Pneumatic-free options. By eliminating the need for pneumatic systems, ERT conveyors remove a potential source of contaminants.
- Belt-free design. The absence of a continuous belt eliminates a major source of particle generation caused by friction.
Perhaps most importantly, ERT conveyors are ISO Class 4 verified for cleanrooms*, making them suitable for even the most stringent clean manufacturing environments.
Flexibility and Customization
Medical device manufacturing is not a one-size-fits-all industry. From tiny hearing aids to complex diagnostic equipment, the range of products and processes is vast and varied. This diversity demands conveyor systems that can adapt to different product sizes, shapes, and production requirements.
ERT conveyors shine in their ability to meet these diverse needs:
- Adaptable configurations. The modular design of ERT systems allows for easy customization to fit specific product dimensions and production layouts.
- Multi-lane capabilities. ERT conveyors can be configured with multiple lanes, accommodating different product sizes or enabling parallel processing.
- Easy reconfiguration. As production needs change, ERT systems can be quickly modified or expanded without requiring a complete overhaul of the existing setup.
This flexibility not only accommodates current production needs but also future-proofs manufacturing lines against changing product designs or production processes.
Improving Efficiency and Throughput
ERT conveyors contribute to enhanced efficiency and increased throughput in several key ways:
High-Speed Capabilities
ERT conveyor systems are designed to operate at high speeds without compromising precision. This allows for rapid movement of products through various stages of production, significantly reducing overall manufacturing time.
Minimized Downtime
The ERT system’s belt-free open-frame design creates less wear on moving parts and gives easy access to the drive components for maintenance.. This simplification leads to several benefits:
- Reduced maintenance requirements
- Quicker line changeovers
- Increased overall system reliability
These factors combine to minimize production interruptions, allowing for more consistent and efficient operations.
Continuous Flow Production
One of the notable features of ERT conveyors is their non-contact zoning capability. This allows for:
- Product accumulation without halting the entire production line
- Independent control of different sections of the conveyor
- Optimized production flow, especially in multi-stage manufacturing processes
By enabling continuous flow, ERT systems help maintain a smooth production process, essential for meeting demanding production schedules in the medical device industry.
Ensuring Gentle Handling of Sensitive Components
Medical devices often contain delicate components that require exceptionally careful handling during the manufacturing process. ERT conveyors are engineered to provide this level of care:
Low Back Pressure Accumulation
This feature is particularly important for preventing damage to sensitive products:
- It allows products to accumulate on the conveyor without exerting excessive force on each other
- Reduces the risk of component damage during temporary stops or slowdowns in the production line
- Particularly beneficial for devices with fragile external structures or sensitive internal components
Customizable Zoning
The ability to create independent zones on the conveyor offers several advantages:
- Products can be moved or stopped as needed without affecting others on the line
- Allows for varying speeds and handling techniques for different products or production stages on the same conveyor
- Enables precise control over the movement of each product, crucial for delicate assembly processes
Static Dissipative Measures
Many medical devices contain electronic components that are sensitive to static electricity. ERT conveyors address this issue through:
- Static dissipative pallet skirts
- Grounded components to prevent static buildup
- Materials selection to minimize static generation during product movement
These features help protect sensitive electronic components from static discharge during transport, reducing the risk of damage or malfunction.
Impact on Production Efficiency and Quality
The combination of increased efficiency and gentle handling provided by ERT conveyors can have a significant impact on medical device manufacturing:
- Increased production rates without compromising product integrity
- Reduced instances of product damage during manufacturing, leading to lower scrap rates
- Improved consistency in product quality due to controlled handling throughout the production process
ERT conveyors offer a sophisticated solution to the dual challenges of efficiency and careful handling in medical device manufacturing. By providing high-speed capabilities, minimizing downtime, enabling continuous flow, and ensuring gentle product handling, these systems contribute significantly to optimizing production processes in this critical industry.
Integration with Industry 4.0 Technologies
As the manufacturing world moves towards greater digitization and automation, conveyor systems must keep pace. ERT conveyors are designed with Industry 4.0 in mind:
- Automation compatibility. ERT systems integrate seamlessly with robotic systems and other automated production equipment.
- Data collection and analysis. Advanced sensors and controls integration allow for real-time data gathering on system performance and product flow.
- Predictive maintenance. The ability to incorporate system monitoring technology allows for performance tracking can help predict maintenance needs, reducing unexpected downtime.
By embracing these technologies, ERT conveyors help future-proof medical device manufacturing operations, ensuring they remain competitive in an increasingly digital landscape.
Regulatory Compliance and ERT
The medical device industry is heavily regulated, with stringent standards to ensure product safety and efficacy. Key regulations include ISO 13485, which specifies requirements for a quality management system in medical device manufacturing.
ERT conveyors support regulatory compliance in several ways:
- Consistent performance. The precise control offered by ERT systems helps maintain consistent production quality.
- Traceability. Integration with data collection systems supports the traceability requirements of many medical device regulations.
- Documentation support. The ability to monitor and record system performance aids in the documentation processes required for regulatory compliance.
Sustainability in Medical Device Manufacturing
As sustainability becomes an increasingly important consideration in all industries, medical device manufacturers are looking for ways to reduce their environmental impact. ERT conveyors contribute to more sustainable manufacturing practices by helping to ensure:
- Energy efficiency. The system utilizes 24V DC motors on all drives and modules. Combined with its low-friction technology, this design significantly reduces energy consumption compared to conventional conveyor systems.
- Reduced waste. The precise handling and control offered by ERT systems can lead to fewer rejects and less material waste.
- Longevity. The durable design and easy maintenance of ERT conveyors contribute to a longer operational life, reducing the need for frequent replacements.
“As we look to the future of medical device manufacturing, the integration of AI with ERT conveyor systems is particularly exciting. This convergence of conveyor technology and artificial intelligence will be a cornerstone of smart factories in the medical device sector.” – Dorner expert
Comparative Analysis: ERT vs. Other Advanced Conveyor Technologies
While ERT conveyors offer significant advantages for medical device manufacturing, it’s important to consider how they compare to other advanced conveyor technologies. Here’s a brief overview:
- Belt conveyors. While traditional belt conveyors offer simplicity and cost-effectiveness, they may not match the cleanliness and precision control of ERT systems.
- Vacuum conveyors. These offer excellent product control but may be less flexible and more energy-intensive than ERT systems. Additionally, the use of air controlled product handling limits compliance capabilities for clean room applications.
- Magnetic conveyors. While great for metal components, they lack the versatility of ERT for handling a wide range of materials.
ERT conveyors particularly excel in scenarios requiring high precision, cleanliness, and flexibility — key requirements in medical device manufacturing. However, the best choice always depends on the specific application and requirements of each manufacturing process.
Edge Roller Technology (ERT) conveyors represent a significant advancement in medical device manufacturing. By offering unparalleled precision, maintaining cleanliness, enhancing efficiency, and supporting regulatory compliance, ERT systems address the key challenges faced by the industry.
How Dorner Can Help You
As medical device production continues to evolve, driven by technological advancements and changing healthcare needs, conveyor systems like ERT will play a crucial role in shaping the future of manufacturing. Their ability to adapt to new requirements while maintaining the highest standards of quality and efficiency positions them as a key technology for forward-thinking manufacturers.
To learn more about how Dorner’s ERT solutions can revolutionize your medical device manufacturing process, contact our team of experts today. Let us help you build a production line that’s ready for the challenges and opportunities of tomorrow’s medical device industry.
*Note: ISO Class 4 verification based on testing performed by Dorner in 2018. No claims are made regarding the rating of the modular, or tubular welded frames. Further manufacturing processes or modifications to the conveyor may affect the clean room rating. For more information, please contact Dorner engineers for specific application requirements.
FAQs
How do ERT conveyors ensure precision in the production of complex medical devices?
ERT conveyors ensure precision through individually motorized rollers and independently controlled zones, allowing for accuracy in product movement and placement. This system provides precise start/stop control and smooth transitions, crucial for complex medical device production.
What role do ERT conveyors play in maintaining regulatory compliance in medical device manufacturing?
ERT conveyors support regulatory compliance by maintaining consistent production quality and enabling traceability through integrated data collection systems..
How does the edge-driven movement of ERT conveyors minimize contamination risks?
The edge-driven movement of ERT conveyors minimizes contamination risks by reducing surface contact with products and eliminating continuous belts, major sources of particle generation. This design, combined with cleanroom-suitable materials, significantly reduces potential contamination points in the production process.
What are the energy efficiency benefits of using ERT conveyors in medical device production?
ERT conveyors in medical device production offer energy efficiency through 24V DC motors on all drives and modules, resulting in lower power consumption. Their precise control and efficient operation also reduce energy waste and cooling requirements, contributing to overall energy savings.
How do ERT conveyors support Industry 4.0 technologies in medical manufacturing?
ERT conveyors support Industry 4.0 technologies by seamlessly integrating with robotic systems and providing real-time data collection on system performance and product flow. This integration enables predictive maintenance and supports flexible, reconfigurable production lines for adaptive manufacturing in the medical device industry.