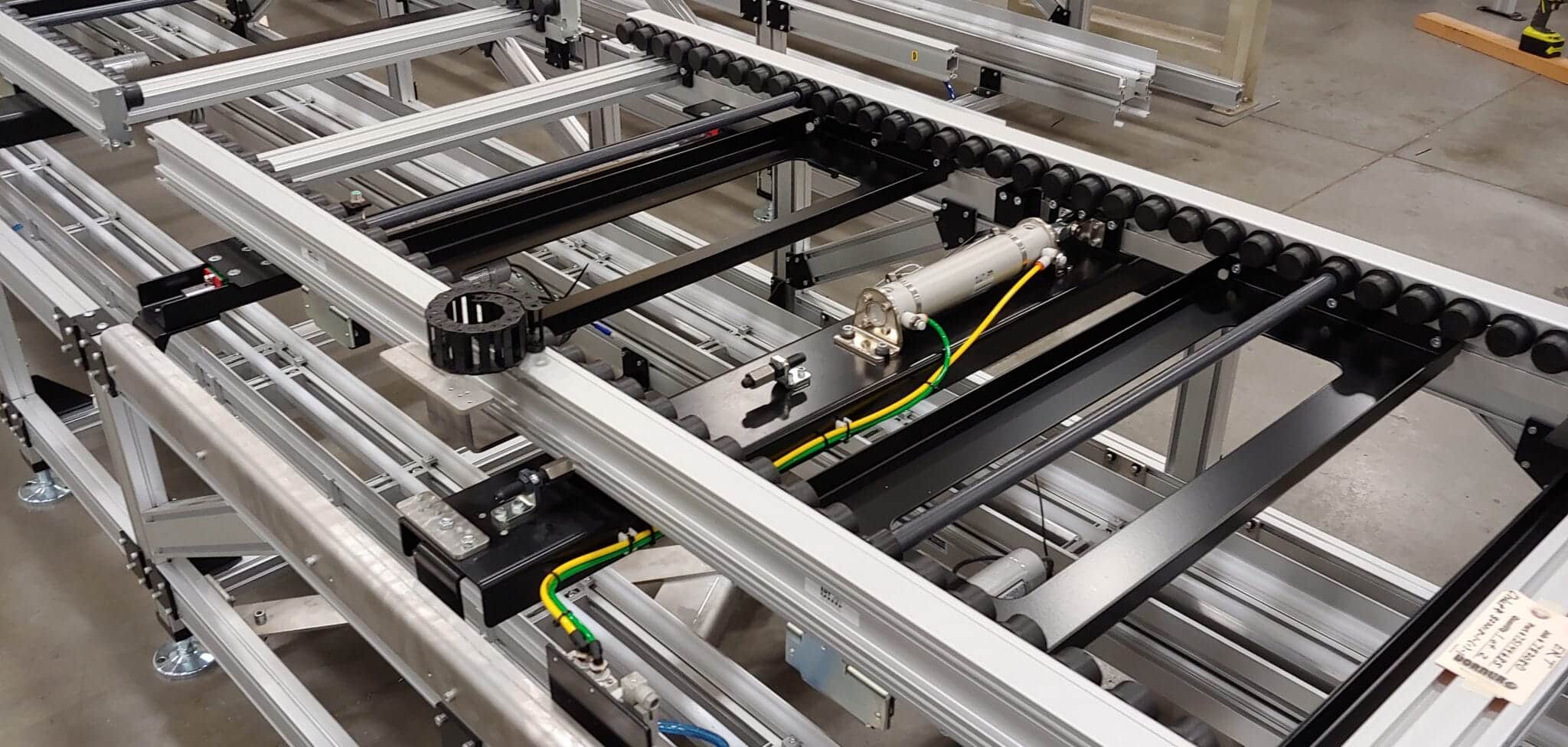
Recently, Dorner provided an extensive custom conveyor solution for a customer looking to assemble large appliances. The system, designed by Dorner’s Engineered Solutions Group utilizes a series of ERT250 pallet handling conveyors that send a part through both manual and automated assembly stations then returns the pallet back to the beginning of the line.
At the core of this system were ERT250 conveyors. Each individual ERT250 conveyor for this application is 32 inches wide and 84 inches long, and includes two gear motors to support the 300 lb load. The only non-standard feature of these conveyors were the stands, which needed to support a lower return conveyor below the ERT. The ERT250 conveyors were connected along the line for a total of 125 feet.
While the ERT250 conveyors remained fairly standard, the pallets were entirely customized to fit the application. These pallets were engineered to fit 20 different part sizes, including some part sizes that are wider than the size of the conveyor. Dorner’s Engineered Solutions Group worked to create a simple, adjustable solution that could cater to both multiple lengths and widths.
The system begins with the large appliance part loaded on to a custom pallet which is then scissor lifted on to the main ERT250 line. The pallet then enters an automated assembly area which is off the main line. Within this area is a three-way Lift and Transfer module that is custom engineered to be low profile so it does not interfere with the lower return conveyor. Once the part has completed the automated assembly Lift and Transfer station, it then moves back to the main line.
Once the pallet returns to the main line it meets a series of Lift and Manual Rotate modules, and In-Conveyor Lift manual assembly stations. Both of these modules were engineered with the goal of improving operator ergonomics. The Lift and Manual stations pneumatically lift the pallets, then operators can turn the pallet 360 degrees for better access to the part. This serves as a cost-effective method for easier assembly. The In-Conveyor Lift is directly integrated with the ERT250 conveyor and is able to lift the pallet 18 inches higher for improved ergonomics during assembly. Additionally, the In-Conveyor Lift was surrounded with a covering for improved operator safety.
As the large appliance completes assembly, it reaches the end of the line where it is then removed and the pallet is then lowered with a second scissor lift. The second scissor lift proceeds to transfer the empty pallet onto the lower return conveyor where it is transported back to the beginning of the line. The lower return conveyor was completed with dual 3200 Series Modular Belt Conveyors that provided a lower-cost option for simple transport.
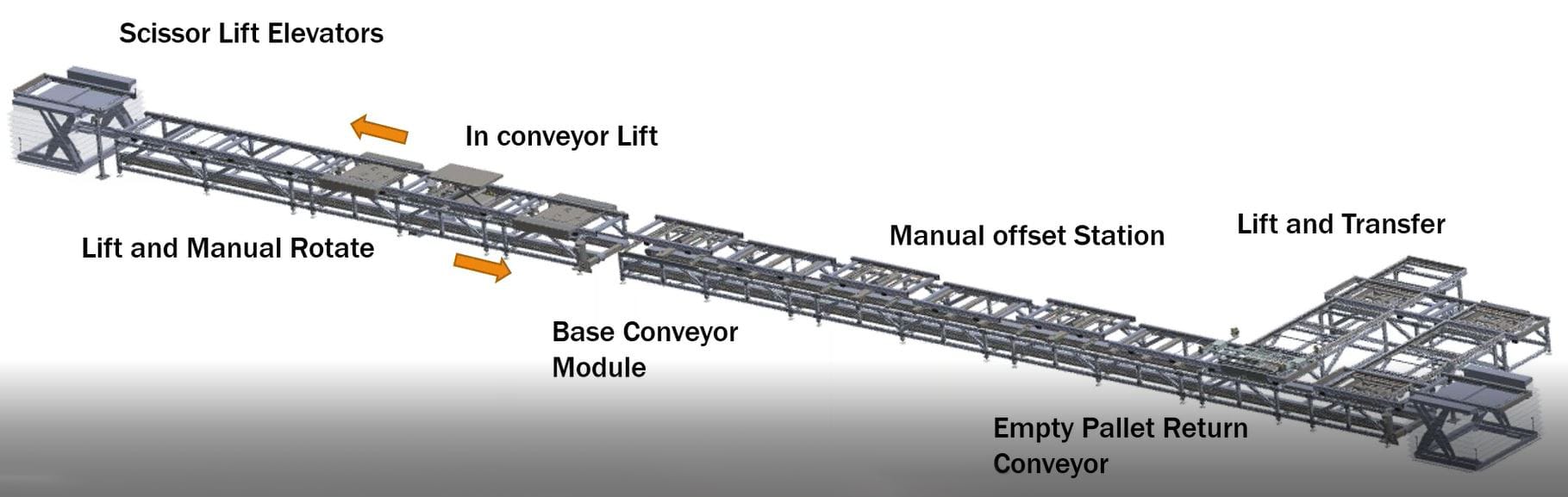
The ERT250 conveyor served as the right solution for this application due to its modular nature and load carrying capability. Not only is the ERT250 significantly quieter, but it also is cleaner than other belted pallet conveyors due to reduced friction. The open roller design of the ERT250 also creates a more forgiving environment. Many times bolts, nuts, and other small parts become trapped within the belts or openings of a conveyor and can damage the system. The open roller design of the ERT250 allows for parts to drop straight through instead of becoming trapped.
Additionally, to further customize the system Dorner engineered a 60ft 3200 Series Shuttle Cart for precise part offloading. As the cart rides along the track, it precisely stops at nine different stations to unload the part for that stage of production. This is yet another example of Dorner’s Engineered Solutions Group capabilities.
Having conveyor solutions that are molded for your business’ exact workflow is critical. Your production line’s performance affects your bottom line. With custom-designed conveyor systems in place, your products will be processed faster, your services will be delivered faster and your profits will increase. Contact Us to get started with finding your own custom conveyor solution.