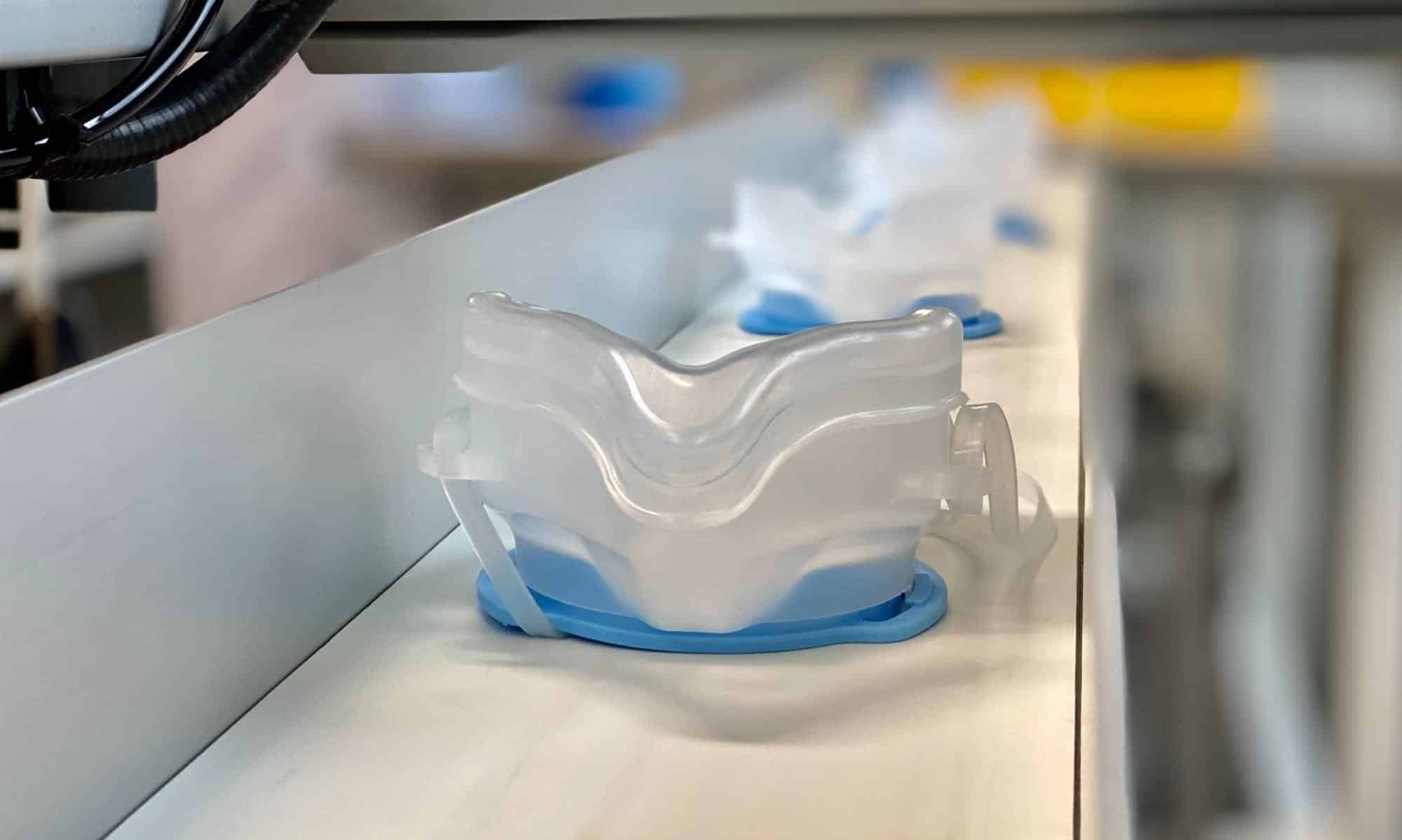
With new medical discoveries being made seemingly every day, the medical device industry must quickly evolve to create new and innovative devices that progress with the medical industry. As manufacturers work to develop new products and keep up with industry demands, automated conveyance, and production tools are becoming essential to help scale operations, improve product quality, and increase efficiency in the medical device production line. Here are five key benefits of integrating automated precision conveyors into your production line:
Enhanced Precision and Accuracy
Automated precision conveyors are designed to handle delicate and complex components with exceptional accuracy. This is crucial in medical device manufacturing, where even the slightest deviation can impact the functionality and safety of the final product. The latest conveyance technology from Dorner and montratec features pallet conveyors capable of accurately positioning components within millimeters (and even microns) for the highest accuracy in robotic interfacing. By automating the transportation and positioning of components, these conveyors ensure consistent precision, reducing the risk of errors and improving product quality.
Increased Efficiency & Throughput
Automated pallet conveyance solutions improve production line efficiency and speed by reducing the time and labor needed to transport parts and components between manufacturing processes. With the continuous operation capabilities and low downtime that automated conveyors provide, medical device production facilities can run around the clock to keep up with the healthcare industry’s ever-growing demands.
Improved Quality Control
Maintaining strict quality standards is vital to ensure medical devices function properly and are safe for users. Integrating cleanroom-rated conveyors into a production line means delicate electronics will be transferred through manufacturing without risking damage, and sterile components remain uncontaminated by particles often created by non-compliant machinery. The low-profile medical device conveyors from Dorner and montratec are also easily integrated into quality control systems for thorough inspection and monitoring to ensure all devices on the line function as intended and accurately represent the manufacturer’s quality standards.
Flexibility & Adaptability
As the medical device industry evolves, manufacturers need equipment that can adapt to new products and processes. Automated pallet conveyors offer increased flexibility in handling various types of medical devices and components, and their modular design is easily reconfigured to accommodate the changing needs of medical device production. This adaptability is essential for manufacturers to scale their operations or introduce new products. The ability to seamlessly add onto an existing conveyor line or reprogram automation systems for new processes means manufacturers can grow their production capabilities with minimal downtime.
Lower Cost of Ownership
While the initial investment of automated pallet conveyors can be high, the long-term savings and cost-benefit means companies can expect a reduced overall cost of ownership compared to predominantly manual processes. Precision conveyors from Dorner and montratec are designed for longevity and easy maintenance, helping to reduce the potential downtime for repairs or scheduled maintenance. Additionally, the ERT Pallet Conveyor and montrac® Systems are pneumatic-free and feature energy-efficient 24V DC motors, reducing operational energy consumption costs.
Automated Precision Conveyors: An Investment for the Future
By leveraging the benefits of automated precision conveyors, medical device manufacturers can achieve higher efficiency, better quality, and greater cost savings. As the industry continues to evolve, embracing automation will be key to staying competitive and meeting the growing demands of the healthcare industry. By choosing conveyors from Dorner and montratec, manufacturers can meet the stringent demands and regulations of medical device production while maintaining flexibility and precision in their operation.