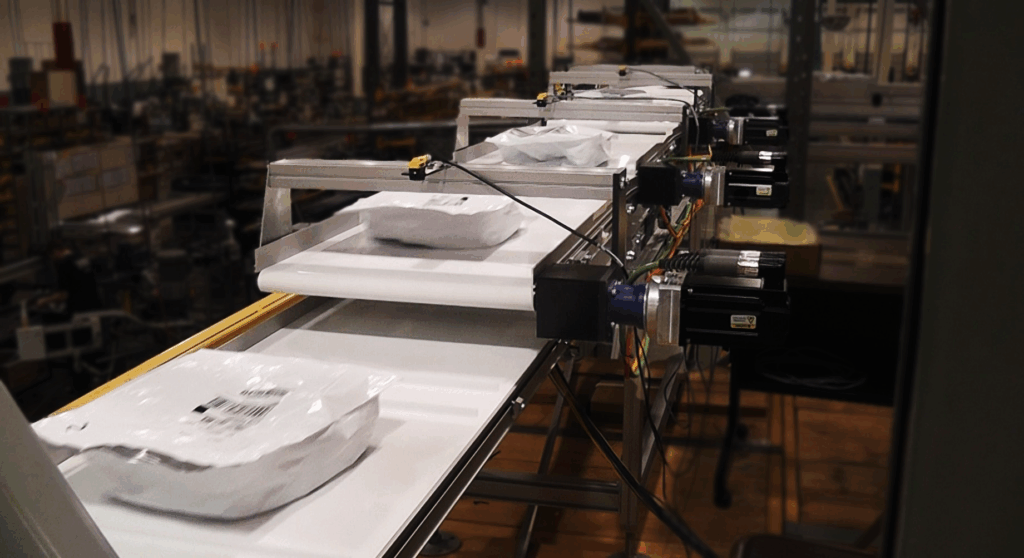
Smart Material Handling Conveyors for E-Commerce and Distribution Centers
Distribution centers and e-commerce operations face unprecedented challenges in today’s fast-paced market. High-volume order processing, diverse product sizes, and rapid
Distribution centers and e-commerce operations face unprecedented challenges in today’s fast-paced market. High-volume order processing, diverse product sizes, and rapid
In today’s fast-paced production environments, maximizing space and efficiency is more crucial than ever. Dorner’s newest addition, the FlexMove Retractable
The landscape of modern warehousing has undergone a remarkable transformation since the first conveyor belt systems revolutionized material handling operations
In today’s fast-paced manufacturing and packaging environments, maintaining efficient product flow is critical to maximizing throughput and minimizing downtime. Accumulation
The C3 Compact Curve Conveyor is a game-changing solution designed to optimize packaging processes across the packaged food industry. By
The C3 Compact Curve Conveyor can be utilized in a bakery production facility needing to handle unpackaged and packaged bakery
Reinforces CMCO’s growing leadership position in the fast-growing electrification and battery production vertical end market Reports fourth consecutive quarter of
Curved conveyor systems are crucial in many production lines—particularly those dealing with delicate or complex materials that must navigate turns
Industrial conveyor systems have become an indispensable part of manufacturing automation, serving as the backbone for many modern production lines.
Behind the Conveyor – Team Spotlight Dorner has become a global brand in conveyor automation – and that’s all thanks
Conveyor belts have long been the heart of modern manufacturing, logistics, and distribution. From speeding up product handling to improving
Small conveyor belts are revolutionizing the way companies handle product movement in industrial automation, medical device manufacturing, e-commerce, and more.
It is that time of year again for Pack Expo International! The Dorner team has been working hard for months
Behind the Conveyor – Team Spotlight Dorner has become a global brand in conveyor automation – and that’s all thanks
In the world of automated guided vehicles (AGV) and montrac® shuttle conveyors, there are several misconceptions to be addressed. Let’s
Behind the Conveyor – Team Spotlight Dorner has become a global brand in conveyor automation – and that’s all thanks
HARTLAND, Wis., (August XX, 2024) — Mark Schmid has been appointed Regional Sales Manager, covering the upper Midwest portions of
Battery Show North America is coming up fast, and the Dorner team is excited to showcase battery and electronics conveyor
The medical device manufacturing industry faces a unique set of challenges. Precision, cleanliness, and efficiency are not just goals —
HARTLAND, Wis., (August 30, 2024) — Tim Patt has been selected as Regional Sales Director for Dorner. In this position,
With new medical discoveries being made seemingly every day, the medical device industry must quickly evolve to create new and
We are happy to announce some new features to our FlexMove flexible chain conveyance solution. These additions further the complete
Behind the Conveyor – Team Spotlight Dorner has become a global brand in conveyor automation – and that’s all thanks
Leading meat producers are continuously challenged to improve production line efficiency while adhering to the stringent hygiene standards of the
Ready-to-eat foods have come a long way since the TV dinners of our parents’ and grandparents’ childhoods. From compartmentalized aluminum
Recently, Dorner Europe helped create a unique conveyance system for Pfeifer & Langen, a leading sugar manufacturer in Europe. The
Behind the Conveyor – Team Spotlight Dorner has become a global brand in conveyor automation – and that’s all thanks
At Dorner we are committed to constant innovation and improvement to meet the evolving needs of our customers. We are
It’s that time of year again for Automate! This year, the Dorner team is excited to join our new Conveyance
The AquaGard GT offers a truly unique conveyance solution for packaged food and beverage applications. Utilizing a flexible chain belt
Dorner - Global Headquarters
Products
Industries
Quick Links
© 2024 Dorner Mfg. Corp. All Rights Reserved | Privacy Policy